Introduction (Approximately 100 words):
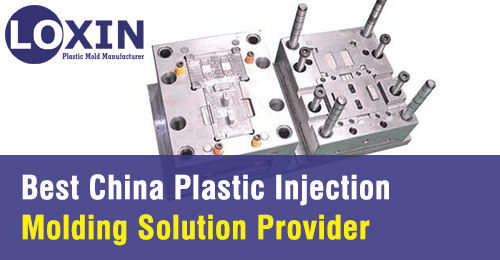
Injection molding is a highly versatile manufacturing process that has revolutionized the production of plastic parts across various industries. However, ensuring optimal part quality throughout the process can be challenging. It requires not only advanced technologies but also a deep understanding of the complexities involved. In this blog, we will explore the significance of parting line injection molding and discuss how it influences the overall quality of plastic parts.
Understanding Parting Line Injection Molding (Approximately 200 words):
In injection molding, the parting line refers to the interface or the separation point where the two halves of the mold meet. It is essential for creating complex geometries and intricate designs in plastic parts. During the injection molding process, molten plastic materials are injected into the mold cavity, which is defined by the parting line. Once the plastic cools and solidifies, the mold is opened, and the part is ejected.
However, the parting line can impact the quality of the final product. Inefficient parting line design can lead to several issues, including warpage, weld lines, sink marks, and flash. These defects not only compromise the aesthetics but also affect the structural integrity and functionality of the part. Therefore, it is crucial for manufacturers to invest in optimizing parting line injection molding to ensure consistent quality.
Predicting and Problem-Solving for Warpage (Approximately 300 words):
Warpage is a common challenge in injection molding, where the plastic part deviates from its intended shape or form. It occurs due to internal stresses caused by uneven cooling, shrinkage, and material properties. Warping can affect the functionality and dimensional accuracy of the part, leading to costly rejections and delays.
To overcome this issue, advanced simulation software, such as Autodesk Simulation (remove brand name) comes into play. This software employs sophisticated algorithms and analyzes multiple variables to accurately predict potential warpage issues during the design phase. By simulating the injection molding process, including cooling and material flow, engineers can identify potential hot spots, optimizing parting line design, and reducing the risk of warpage. This enables manufacturers to save time, minimize rejections, and maximize part quality.
Solving Weld Lines for Enhanced Part Strength (Approximately 300 words):
Weld lines are another critical factor to consider in part quality optimization. These lines form when two or more fronts of molten material meet, resulting in a visible line or mark on the surface of the part. Weld lines can weaken the structural integrity of the part and compromise its functionality, especially in load-bearing applications.
Predicting the occurrence of weld lines and finding an optimal parting line design can be a challenging task. However, advanced simulation software provides manufacturers with invaluable insights. By accurately simulating the injection molding process, engineers can identify potential weld line formation locations and optimize the part design accordingly. This includes adjusting the gate locations, modifying mold design, or altering the material flow rates to mitigate weld line defects.
Conclusion (Approximately 100 words):
Optimizing part quality in injection molding is crucial for meeting project budgets, schedules, and maintaining customer satisfaction. As we explored in this blog, efficient parting line injection molding plays a pivotal role in achieving the desired quality standards. By leveraging state-of-the-art simulation software, manufacturers can predict and address potential warpage and weld line issues during the design phase. This proactive approach allows for better material selection, enhanced part strength, reduced rejections, and ultimately, better project outcomes. Stay tuned to explore more insights into the fascinating world of plastic part quality optimization!